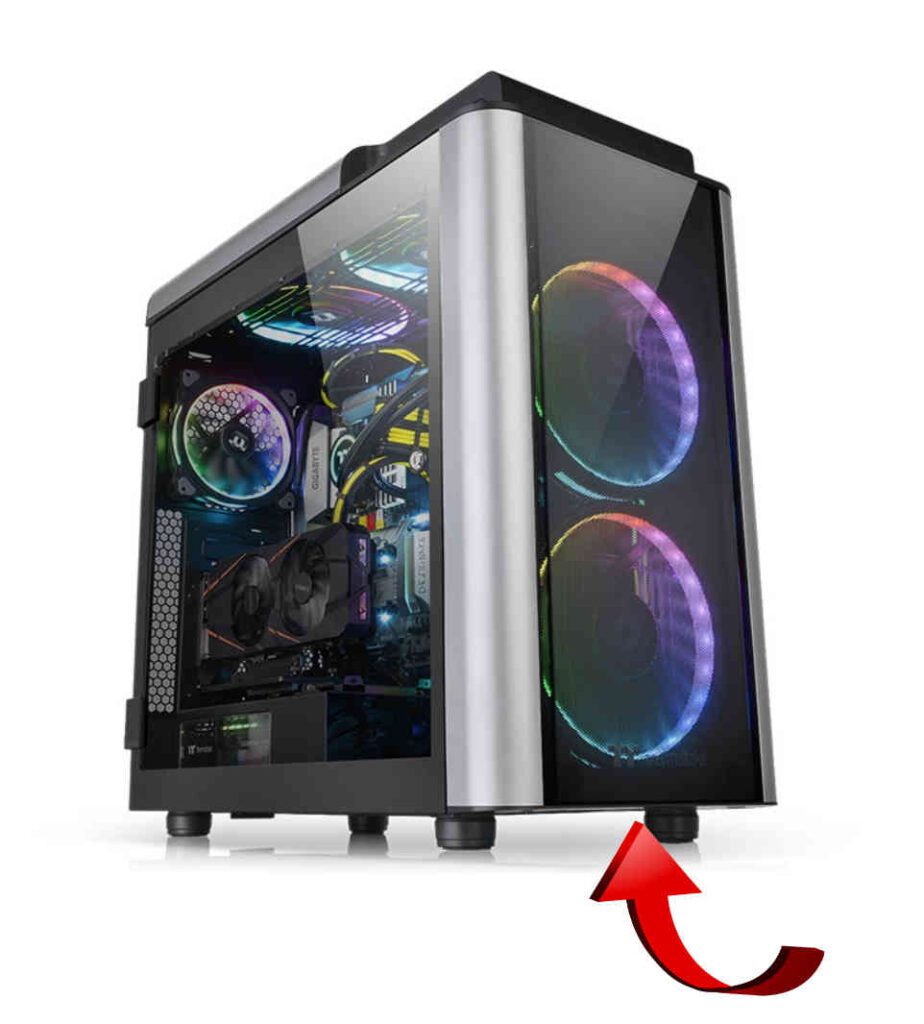
I’ve mentioned before, but I build my own PCs. I began doing it nearly 30 years ago, when one of my early PCs broke down.
In those days, unless you could afford one of the business computers from the big manufacturers (which were hugely expensive), you’d usually get your machine from one of the many popup PC manufacturers which started appearing. Back then, we also had a recognisable high street, and many vendors had shops you could visit to order your machine. They were very affordable – but I discovered the main reason for that.
I’ve always been into electronics, and expanding these machines was usually one of the first things many owners did, even if they were working. Extra memory, another hard drive or CD-ROM (or maybe just a CD-ROM because you hadn’t got one already). But with ownership, the need to go inside to replace things which had broken also became something you expected sooner or later.
The first time I opened one, I was amazed at how empty the case was (and don’t even get me started on the razor-sharp burrs on the crappy cases). A cut-down motherboard with onboard graphics, and cables to the hard drive, the CD-ROM, and the power supply was all that was in there. Then one time, my PC failed completely and I identified that the power supply (PSU) had blown.
When I contacted the shop, they told me they could get me a PSU and it would cost £80 (I’d fit it myself). But that was far more expensive than what I’d seen in the magazines at that time. PSUs went for maybe £20-£30. The problem was, the PSU in my machine – and most machines sold cheaply those days – was a cut-down import from the Far East. It was smaller than a standard PSU, and could only be obtained either by import, or from someone who’d already imported them (i.e. the people charging £80).
I then realised my machine’s case was a standard tower case, and the place where the PSU sits would take a standard sized replacement. So I bought one, fitted it (all the screw holes still lined up), and the machine was fine again. That was until a year or two later, when it (or whatever machine I had) blew again, and this time it wasn’t the PSU.
That was when I built my first one from scratch. I sourced all of the parts from eBuyer (and have done ever since then), and deliberately specced my machine as high as I could afford so it would last for several years before needing another major upgrade. Since then, I’ve built at least five.
Now we’re getting to the point. The last one, I specced very highly. When I ran the benchmark tests after I powered it for the first time, it was in the top 1% in the world for speed and other features. But I’d also chosen the Thermaltake Level 20 GT case for it.
The Level 20 GT is a beast. Even with nothing added to it, it weights about 20kg, but the full working system is well over 30kg. And that means that unless you live in the most open-plan and minimalist environment (and I don’t), once you’ve put it somewhere you don’t really want to be having to move it out regularly – or in my case, at all, unless it can be avoided. And it is big enough that when you do position it, you don’t want it in the middle of the room. It goes on or under somewhere, next to a wall.
Now, anyone with even a basic understanding of computers that run off the mains and can do fancy things will know that apart from their functionality, they are also effectively big Hoovers. The fans suck in air to blow over the components inside to cool them down. And air contains dust (especially in a bedroom or home office). Over time, that dust collects on the grilles, the fans, and eventually even on the components inside. The grilles and fans are the first to be affected, and if you don’t do anything the airflow is reduced and your PC starts to overheat.
My PC has not overheated. But I had noticed a build up of dust on the front grille covering the front fans. In fact, I first became aware (and moderately concerned) about it a couple of years ago. I tried to removed the front panel, but could see no way except by relocating my 30-40kg monster and partially dismantling it. Yet there were no obvious screws to remove.
I’d Googled it, and the only advice (and not much of it) was that the grille pulled off, but this was confused by other advice that you needed to get at something inside (clips). I was also mindful of the initial assembly of my system, and all the myriad screws necessary to accomplish that – so I was still kind of assuming screws would be involved somewhere. But they aren’t.
I’d tried pulling it before, but I was being very gentle for fear of breaking it. Periodically, I’d had another feel underneath to see if I could find something I’d missed, and had another few gentle pulls to no avail. This is over a period of two or more years, you understand. And trust me, it isn’t in the manual.
But yesterday, I decided to sort it once and for all. Again, I’d seen the advice that it pulls off, and this time I wasn’t so gentle. I gave it a good sharp tug at the bottom (see photo, the arrow shows where there is a grab slot about 3cm back underneath) and it popped out surprisingly easily considering the problems I’d had before. I ran my fingers up the side and pulled at the top and it came off easily.
Once out, the tempered glass panel has to be removed, and this is held by four short screws (so do it on a table). Once these were removed, the glass panel was free and the grille could be cleaned. I used a paintbrush to get the main bulk of dust off, then an air blower to remove the smaller stuff. I could have washed it using water, but it was now completely dust free and so didn’t bother.
Once I’d screwed the glass panel back in, I re-positioned the whole front panel against the case, located the clips into their slots (important), then gave it a sharp tap in each corner to push them back into place.
I simply cannot believe that this has flummoxed me for as long as it has, when it turned out to be so simple.
As a footnote, can I point out that my PC doesn’t have loads of poncey colours flashing all over the place. Mine is a muted red colour.